Nowadays, laying hens are typically raised in battery cages for layers, which offer a relatively healthy and safe production environment, thereby enhancing their egg-laying capacity. Battery cages for layers also help reduce disease transmission and simplify management. However, transferring hens into battery cages must be done correctly, as improper handling can negatively impact their productivity. So, what should we consider when placing laying hens into battery cages for layers? Let’s explore the key points together.
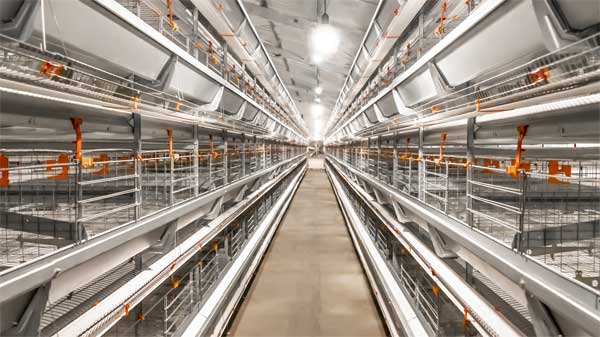
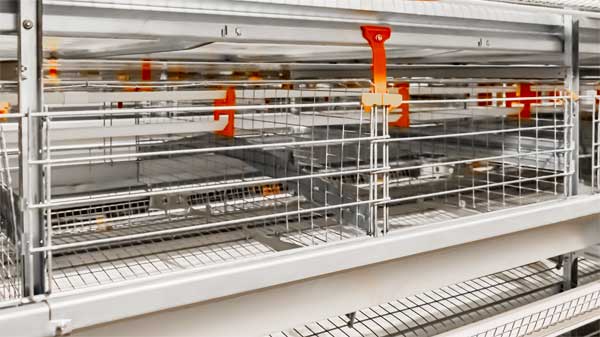
Issues When Transporting Hens into Battery Cage for Layers
Optimal Age for Caging Layer Chickens
The appropriate age for caging layer chickens is generally between 13 and 18 weeks. This age range ensures that the weight of young laying hens is within the normal standard and improve their egg production rate during the breeding process. It is important to note that the caging should not be delayed beyond 20 weeks of age. However, if the chickens are growing well, we can continue to cage them at 60 days old. When caged into battery cage for layers, we also need to group and cage them in batches according to the different growth of laying hens.
Facilities and Equipment
After the laying hens are caged into battery cage for layers, it is crucial to maintain their original growth environment to avoid any negative impacts on their growth and production. We need to equip the corresponding breeding equipment and install various breeding facilities before caged. In addition, it is essential to conduct thorough inspections and replacements of these facilities and equipment to avoid problems in the later breeding process.
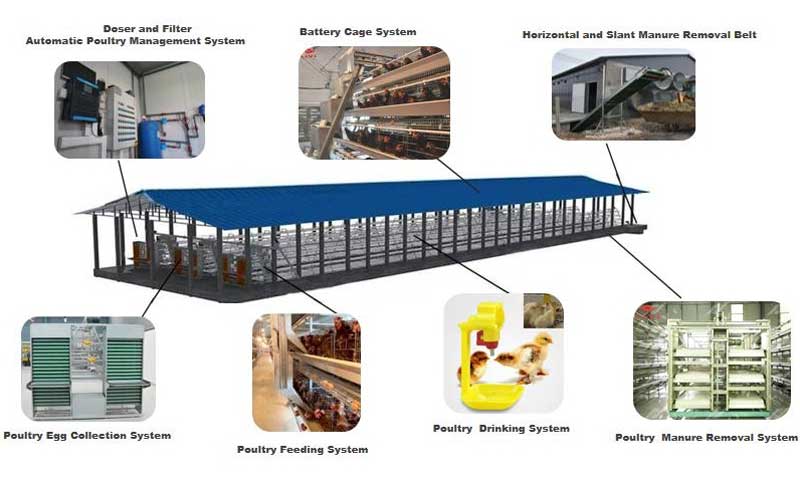
Grouping and Put chickens as Their Commons
When putting laying hens into battery cage for layers, we must be scientific, not make too much noise, be gentle, and not use too much force. Never alarm the chickens, otherwise it will cause an overreaction, which will have a great impact on the growth and production of laying hens. Generally, chickens that are stressed will have a lower appetite, and then they will gradually weaken, seriously affecting the health of the chickens. Group and cage the chickens according to their growth rates, organizing them in different groups and batches to ensure uniform development.
Environment Maintenance
After caging into the battery cage for layers, maintain the chickens’ original growth environment to avoid stress reactions caused by sudden environmental changes. This includes keeping appropriate temperature, humidity, and ventilation conditions, ensuring good air circulation within the coop, and minimizing harmful gas accumulation.
Health Checks
Perform comprehensive health checks on the chickens before caging to identify and address any potential health issues, such as diseases or malnutrition. Regular health checks help detect problems early and take corrective measures to ensure the flock’s health and productivity.
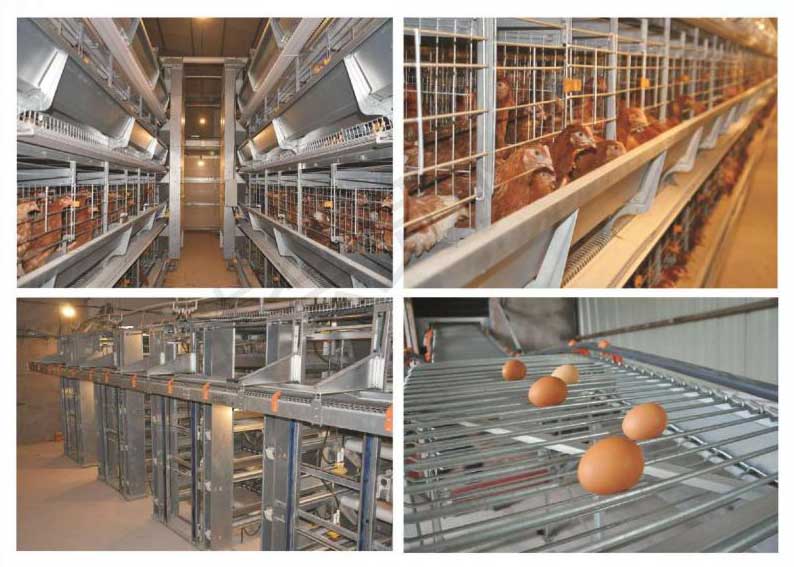
Continuous Monitoring
Continuously monitor the chickens after caging, observing their behavior, eating, drinking, and excretion patterns. Early detection of stress reactions or health issues allows for timely adjustments in management practices, such as feed formula changes or environmental improvements, ensuring the chickens adapt well to their new environment and maintain high production capacity.
Agico is a manufacturer of poultry cages, especially battery cage for layers, specializing in research and development, production, sales, installation, and after-sales service of battery cages. Our main products are: layer chicken cages (including brooding, laying hens, broilers, laying ducks, meat ducks), automated breeding equipment, Cage Free Chicken House, fully automatic egg collection equipment, fully automatic feeding system, manure cleaning series, farm intelligent environment controllers, and fans, water curtains, manure extractors, hot air furnaces and other breeding equipment.
The battery cages produced by our company have the characteristics of reasonable structure, stable performance, sturdiness and durability. The battery cage for layers adopts hot-dip galvanizing surface treatment technology, and the normal service life of the equipment is more than fifteen years.